
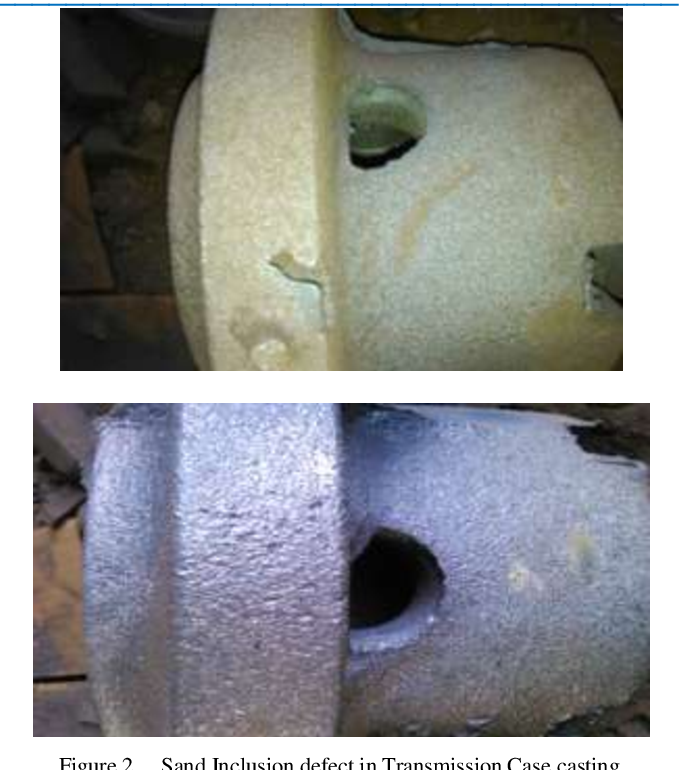
fettling costs) due to higher quality castings with excellent surface finish characteristics. This also reduces cleaning room costs (i.e. This unique compaction method ultimately helps to reduce veining defects. This creates space for silica sand to fill during expansion. All things considered, VEINO offers quality, performance and minimal investment – an excellent choice for most applications.ĭuring casting, the metal heat burns out the starch particles within VEINO.
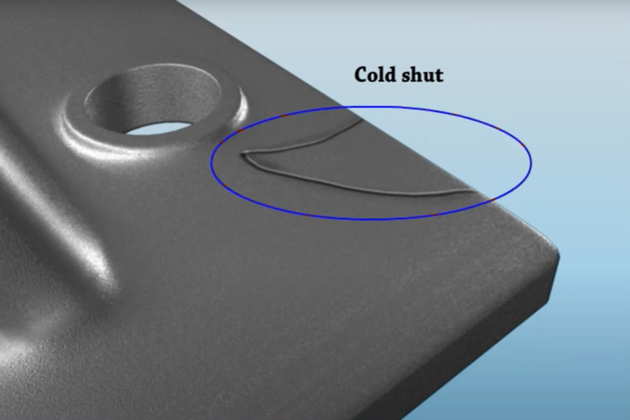
Performance remains unaffected and the flowability rate of VEINO, which leads to good core compaction, is exceptional. This reduced additive consumption level is the lowest in our portfolio and thus leads to cost savings. Our organic and renewable VEINO line is a high-performance additive with an extremely low addition rate. Ultimately, coating-free production offers reduced material costs alongside the elimination of peripheral coating equipment, resulting in major savings. Dimensional accuracy compliance is equally relevant where additives may substitute coatings in thin-walled castings. Within cold box production, in particular, this revelation could reduce costs substantially and enhance productivity. Our engineers – working alongside our customers – are discovering specialty additives that can reduce the use of expensive sands and, in some instances, replace coatings entirely. A small addition, for instance, can remedy several common defects (e.g.

As part of the measures for preventing casting defects, additives are a tried-and-true solution.
